DNX-HD
Channel sizes: 6.4-9 mm (5-10 CPSI). Available with 0.8 mm and 1.0 mm wall thickness. The DNX-HD types are custom formulated with nine different vanadium levels to balance DeNOx activity and SO2oxidation rate to a specified level.
DNX® catalyst features
Topsoe’s DNX® series of catalysts for waste incineration plants features:
- excellent activity at low temperature, allowing SCR operating temperatures as low as 160°C
- a high tolerance towards poisonous elements in the fl ue gas
- possibility to operate below the formation temperature for ammonium bisulfate (ABS) for extended periods
- combined NOx reduction and destruction of gaseous PCDD/PCDF (dioxins and furans)
- elimination of the need for reheating of the flue gas when installed directly after the dust-removal system Topsoe’s DNX® catalysts are based on a porous, fibre-reinforced titanium carrier material impregnated with vanadium pentoxide. A unique manufacturing process provides the catalyst with a well-defined and controlled so-called tri-modal pore structure, featuring pores in three size regimes.
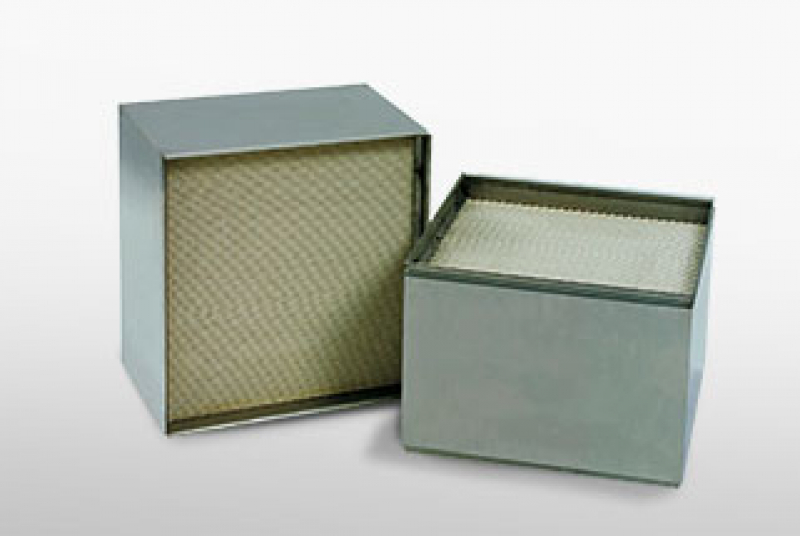
High low-temperature activity
The unique porosity structure of Topsoe’s DNX® catalysts provides a large internal surface area, allowing for a high number of well-accessed active catalytic sites. This results in very high activity, also at low operating temperatures.
High resistance towards poisoning
The optimized pore structure also ensures a large capacity of the DNX® catalyst for accommodating poisons without the normal detriment to activity. This provides an extended service
life of the catalyst even when exposed to dust slip from the ESP or bag filter.
Sub-ABS dew point operation
To reduce or eliminate the need for reheating of the flue gas after de-dusting, the SCR catalyst must be able to operate reliably at temperatures below 250°C. Low-temperature SCR generally requires regular catalyst regeneration due to formation of salts formation, especially ammonium bisulfate, ABS, which is the product of the reaction of injected ammonia with sulfur trioxide and gaseous sulfuric acid present in the flue gas.
The operating time between regenerations depends strongly on the catalyst’s capacity for accommodating ABS while still exhibiting the required activity for the DeNOx reaction to occur.
The high porosity of the DNX® catalysts featuring multi-sized pores secures that even with significant amounts of ABS condensed in the pore system, a high activity is maintained for
an extended period of time.
Experience shows that this unique tolerance towards ABS condensation enables continuous operation below the ABS dew point for months. Thus, with an optimized design of the catalyst
and an operation temperature of e.g. 190°C, the SCR can accommodate for a typical content of sulfur oxides in the flue gas of 5 mg/Nm3.
The regeneration of the catalyst is performed by heating to a temperature well above the ABS dew point temperature. Regeneration with full restoration of catalyst activity is performed
within a few hours at e.g. 350°C.
Destruction of dioxins and furans
Topsoe’s DNX® catalysts also destroy gaseous dioxins and furans (not particle bound) through catalytic oxidation. Destruction efficiencies exceeding 99% can be obtained by
designing the SCR system accordingly, fulfilling e.g. the EU directive emission limit value for the total of dioxins and furans of 0.1 ng/m3. It usually requires a larger, multi-layer SCR system than for just the DeNOx function.
Dioxin/furan destruction requires SCR operating temperatures below 275°C. At higher temperatures there is the risk of dioxin/ furan formation via reactions, so-called de-novo synthesis, of carbon compounds with chlorine compounds over metal oxides, e.g. copper or iron.
Proven performance
Since the mid 1990’s Topsoe has supplied catalyst and engineering for SCR units on waste incineration plants. The experience portfolio covers more than twenty installations, and in all cases convincing fulfilment of design performance has been demonstrated in terms of NOx and dioxin removal efficiencies as well as pressure loss and operating time between catalyst regenerations. This experience combined with our multi-disciplinary know-how ensures that our clients are provided with optimum solutions.